Whether you are looking to produce Automotive Parts Injection Moulds for the first time, or you are already an experienced maker of parts, there are a few things to keep in mind when designing your products. These include the cost-effectiveness of the process, the repeatability of the results, and the versatility of the product.
Choosing the right materials for automotive parts injection molding is a key factor in the manufacturing process. Not doing so can cause issues such as corrosion and heat sensitivity. With the right materials, you can avoid these issues and streamline the manufacturing process.
Various plastic materials are used in the injection molding process. These materials vary in terms of strength, durability, cost, and flexibility. These qualities are mainly determined by the product's end use, service conditions, and regulatory requirements. Choosing the correct materials can improve product performance and efficiency, as well as reduce tooling costs.
Injection molded parts are made of hundreds of different plastic materials. The wrong material choice can result in problems, such as voids, holes, and structural weakness. If you are unsure of what materials to choose for your project, KASO Plastics can help you narrow down your options and make the best choice.
Cost-effectiveness
Using a 3D printed injection mould to produce automotive parts can be a great way to get an end product to market quickly and at a lower cost. These prints are chemically bonded to the material, eliminating the need for post-processing steps, such as demounting, coating, and painting. They can also be integrated into the existing injection molding workflow.
While the technology behind 3D printing may not be new, its ability to cut costs makes it a worthy investment for manufacturers. Not only can it be used to create molds, it can also be utilized to create functional prototypes. It also saves CNC operators and skilled craftsmen from tedious manual tasks.
The process involves the injection of liquid plastic into a cavity in a mold. It is then cooled before ejecting the finished part. The resulting product is a three-dimensional mirror image of the original.
Versatility
Using a plastic automotive parts injection mould is a great way to create a wide variety of parts. This method can be used in a wide range of industries including automotive, aerospace, and medical equipment.
Injection molding is a reliable and precise process that can be applied to a wide range of products. It produces exact copies of a design and can produce a number of different types of parts. It can also be used to manufacture a variety of different materials, enabling you to tailor your part to the needs of your end use.
Injection molding can be a cost-effective solution for producing a wide variety of parts. Typically, it requires a larger upfront investment in molds and tooling, but it can be an efficient way to produce a large quantity of parts in a short amount of time.
Rapid prototyping
Creating a rapid prototyping of automotive parts injection mould requires a few different steps. Depending on the quantity and the material, you will need to determine the best tooling method for your project. If you have a small number of units, then a quick turn mold is likely the best option. If you have a larger number of units, then a CNC machined prototype is the ideal choice.
A rapid prototype of automotive parts injection mould can help manufacturers verify the design and functionality of their new products. It also allows engineers to make improvements on the design as it is being developed. Using a prototype can greatly reduce the time it takes to get a product to market.
A rapid prototype of automotive parts injection mold can help reduce the overall cost of the product development process. It can also speed up the production cycle. This allows designers to catch problems early, which reduces delays in the process. The turnaround time for a prototype can be as short as three days. This can cut the product development cycle in half.
Repeatability
Choosing the best manufacturing process for your automotive parts is crucial to ensuring that your car is both aesthetically pleasing and functional. It is also important to know that repeatability is one of the most important aspects of any production process.
It is essential to have a repeatable process because it will ensure that your vehicle models meet the same specifications every time. This equates to higher quality parts, and a lower cost per part.
To achieve this, engineers must optimize their design for the manufacturing process they are using. This is particularly important when it comes to injection molding, as there is a high level of accuracy involved.
Choosing the right resin is an important aspect of the production process. It is also a good idea to choose a material that can be recycled.
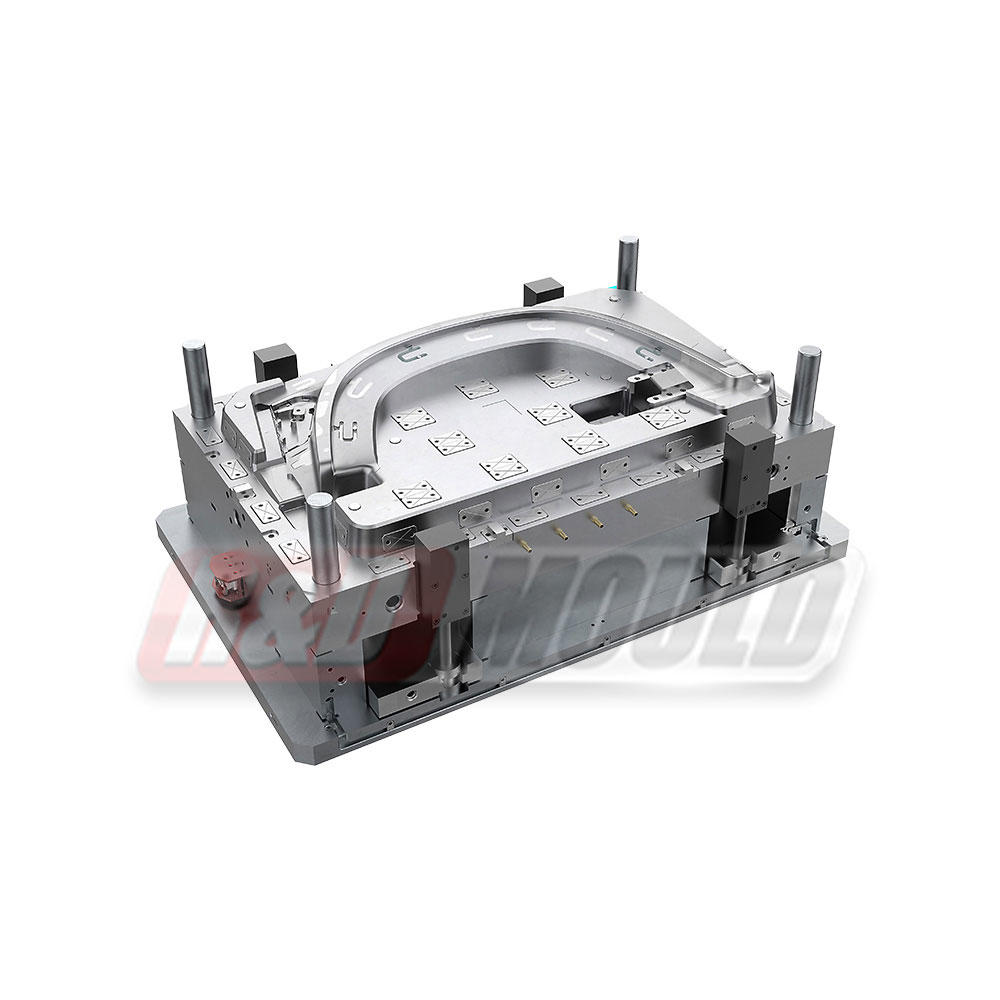
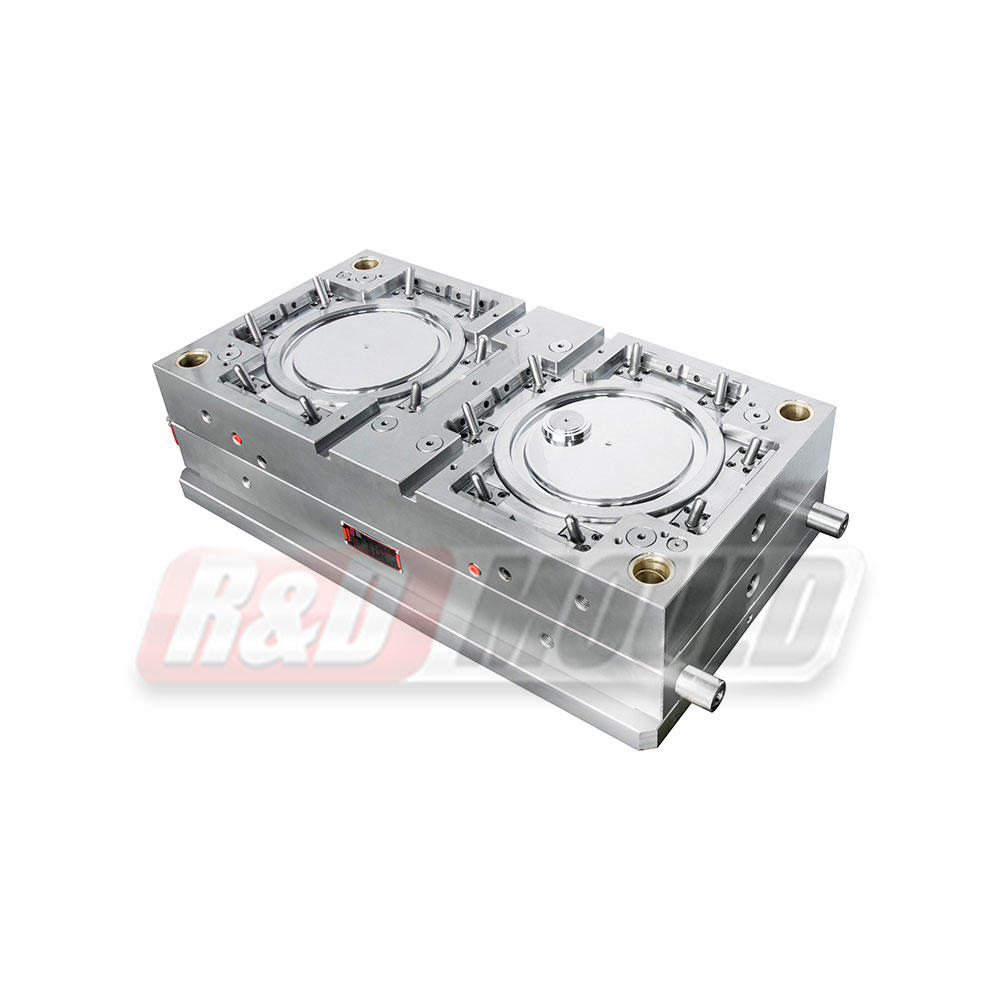