Plastic automotive molds, predominantly made from materials like polyurethane, polycarbonate, and polypropylene, offer several advantages over their metal counterparts. One of the most significant advantages is their lightweight nature, which plays a crucial role in enhancing fuel efficiency and overall vehicle performance. Unlike metal molds, plastics allow for intricate designs and complex shapes, enabling automotive engineers to create innovative and aerodynamic vehicle components that were once deemed unattainable.
The flexibility offered by plastic molds is a game-changer in the automotive industry. Engineers and designers can experiment with various design iterations quickly and cost-effectively, facilitating rapid prototyping and accelerated product development cycles. This flexibility not only expedites the manufacturing process but also enables the creation of vehicles that are visually appealing, functional, and optimized for performance.
plastic molds excel in their ability to withstand high temperatures and pressures during the molding process, ensuring precision and consistency in manufacturing. This reliability significantly reduces production errors and ensures that each part meets stringent quality standards, contributing to overall vehicle safety and reliability.
The cost-effectiveness of plastic automotive molds cannot be overstated. Compared to metal molds, plastic molds are more affordable to produce and maintain, resulting in substantial cost savings for automotive manufacturers. Additionally, the lower tooling costs associated with plastic molds make them an attractive choice for producing vehicle components in smaller volumes or for niche markets, allowing for greater customization without exorbitant expenses.
The application of plastic molds extends across various automotive components, ranging from interior panels and trim pieces to exterior body parts and structural elements. Dashboard components, door panels, bumpers, and even intricate engine parts are now commonly manufactured using plastic molds. This widespread adoption underscores the versatility and adaptability of plastic molds in meeting the diverse needs of the automotive industry.
the environmental benefits of plastic molds cannot be overlooked. These molds are recyclable, contributing to sustainability efforts within the automotive sector. Manufacturers are increasingly focusing on utilizing recycled plastics in mold production, thereby reducing waste and minimizing the industry's environmental footprint.
challenges persist in the realm of plastic automotive molds. Despite their numerous advantages, certain concerns, such as durability and heat resistance, require continuous research and development efforts to address. Engineers are consistently striving to enhance the durability of plastic molds without compromising their lightweight characteristics, seeking materials that can withstand harsh conditions while maintaining structural integrity.
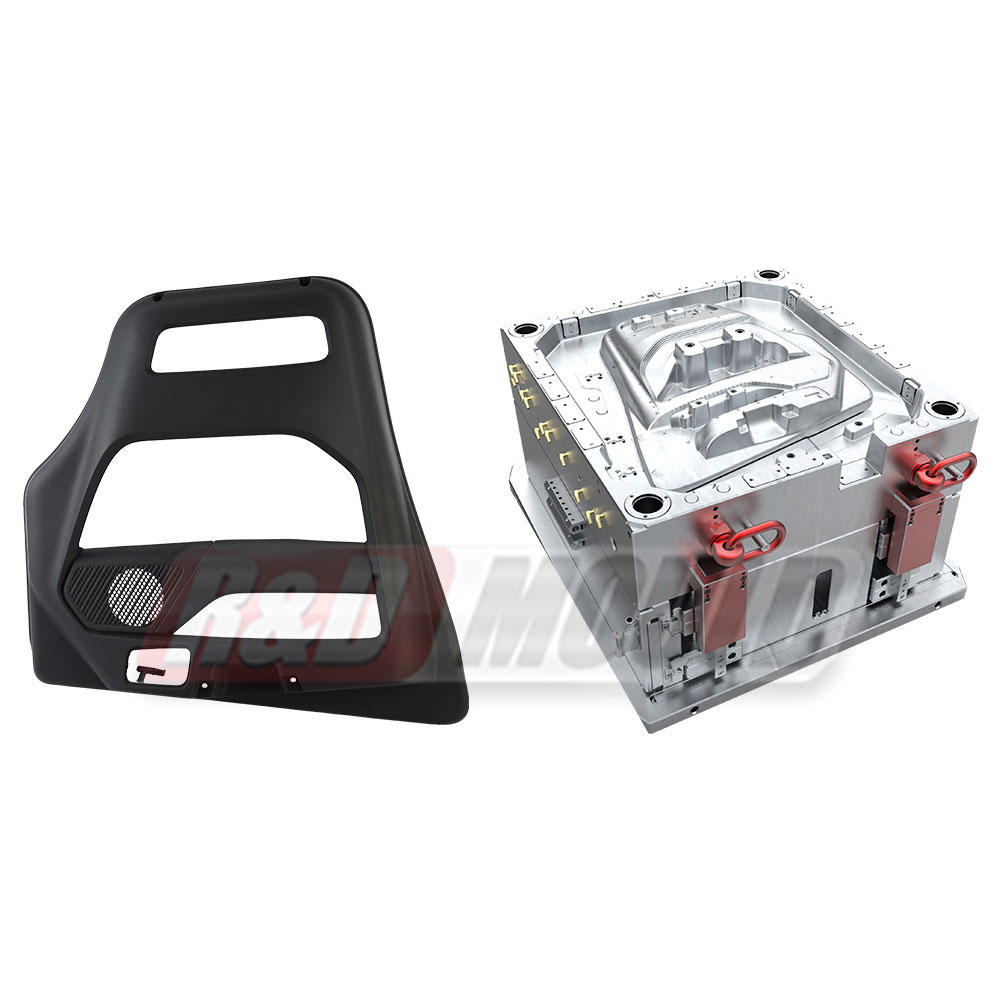