Plastic injection molds are custom-made tools designed to shape molten plastic material into desired forms. They play a vital role in the production of a wide range of plastic components used in various industries, including automotive, electronics, medical, consumer goods, and more. The molds define the size, shape, and surface finish of the final plastic parts, ensuring consistency, repeatability, and precision in large-scale manufacturing processes.
2. The Creation Process of Plastic Injection Molds
Developing a plastic injection mold is a meticulous process that involves several stages, including design, mold-making, and testing. Here is a brief overview of the key steps:
a. Design: Skilled engineers work closely with manufacturers and product designers to create a 3D model of the desired plastic component. Factors such as material selection, part geometry, and functionality are considered during the design process.
b. Mold-making: The mold is fabricated using precision machinery and advanced techniques. High-quality steel or aluminum blocks are machined to form the mold cavities and cores, taking into account the intricacies of the component design.
c. Testing and refinement: The newly created mold undergoes rigorous testing to ensure that it meets the required specifications. Samples are produced to evaluate the part quality, dimensional accuracy, and functionality. Any necessary adjustments or modifications are made to the mold to achieve optimal results.
3. Versatility and Application in Various Industries
Plastic injection molds find extensive application across diverse industries due to their versatility and ability to produce complex parts with high precision. Some notable industries that rely on plastic injection molds include:
a. Automotive: Injection molds are instrumental in manufacturing components such as interior trim, dashboard panels, engine parts, and exterior body parts.
b. Electronics: Molds are used to produce casings, connectors, switches, and other intricate components for electronic devices.
c. Medical: Injection molds enable the production of medical devices, syringes, vials, surgical instruments, and other critical healthcare products with strict quality and safety requirements.
d. Consumer goods: Plastic injection molds play a vital role in creating a wide array of consumer products, including toys, packaging, household appliances, and kitchenware.
4. Benefits of Plastic Injection Molding
Plastic injection molding offers numerous advantages, thanks to the precision and efficiency of plastic injection molds:
a. High precision and intricate designs: Injection molds enable the creation of complex, detailed, and highly precise parts that would be challenging or impossible to achieve with other manufacturing processes.
b. Cost-effectiveness: Once the mold is created, the actual production process becomes highly efficient and cost-effective, as large quantities of parts can be produced quickly and consistently.
c. Material versatility: Plastic injection molding supports a wide range of thermoplastic materials, offering flexibility in material selection based on specific product requirements.
d. Consistency and repeatability: Injection molds ensure consistent part quality and dimensional accuracy, allowing for large-scale production without compromising on quality control.
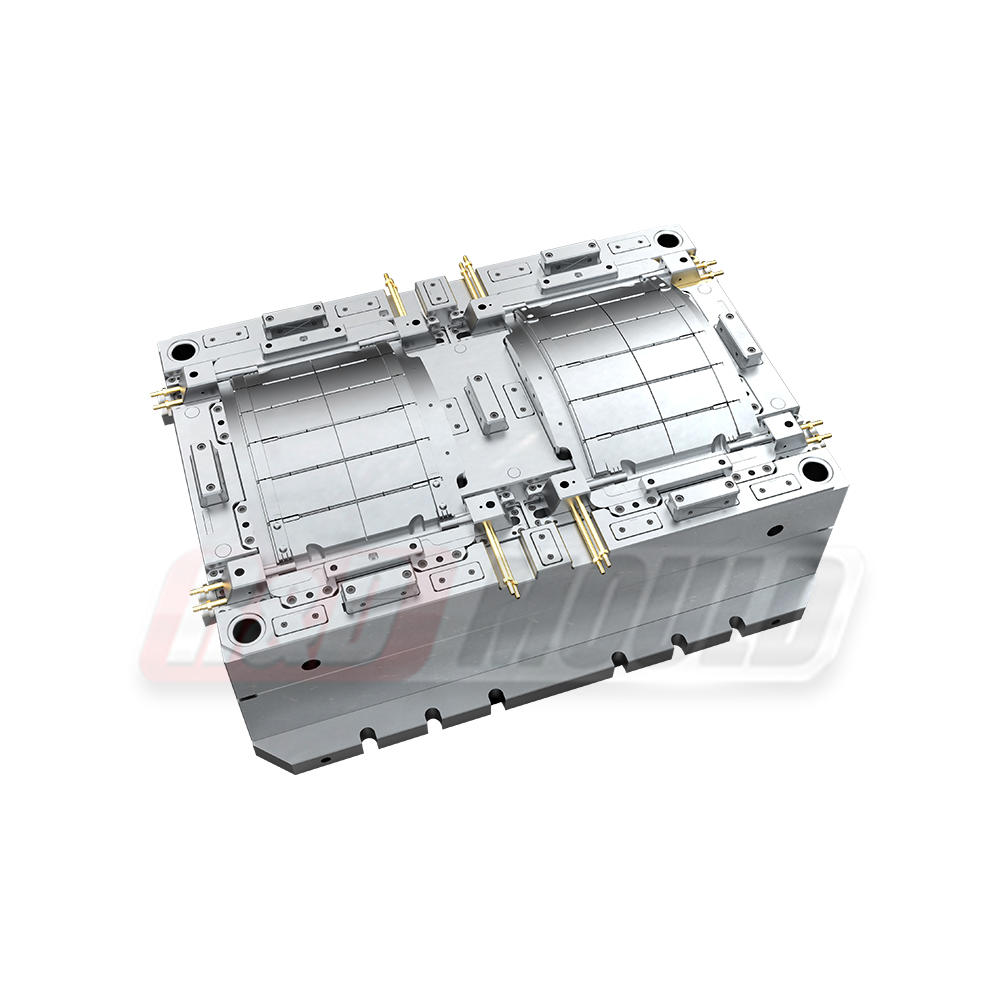