Whether you are looking to develop a new product range or simply add to your existing business, a plastic food container mould will give you the ability to manufacture your food packaging products quickly and efficiently. As the demand for restaurant foods continues to grow around the world, plastic moulds are becoming an increasingly important part of the food service industry. With the right plasticiser and sealing features, your plastic containers will be able to keep your foods fresher for longer, while saving you money.
A wide variety of materials are available for use in food container manufacturing. Common polymers include styrene, polypropylene, and polyethylene. These types of plastics are durable, flexible, and hygienic. They are also able to withstand chemicals. These materials are especially suited for lids and containers.
Silicon is another material that is suitable for food container moulds. It is non-toxic, tasteless, and odorless. It is also less likely to scratch than metals. In addition, it does not dent or shatter. Compared to metals, silicon is ideal for food container moulds.
You will need to select a high-quality plasticiser that provides excellent sealing properties. This will help ensure your containers are hermetically sealed, which will protect your edible goods from air and moisture. Hermetically-sealed containers are great for promotional materials and food line sampling.
A food container mould consists of a base, a molding cavity, and a mold release agent. A mold release agent is applied to the mould to prevent the material from sticking to it. Then, the moulded product is injected into the mould cavity. This process is then allowed to cool. The finished product is then ejected from the machine.
The moulded product should have a minimum of seven 18 mm diameters. The plastic is then coated with a liquid plastic coating that hardens after it has cooled. The finished product is then put through quality control tests. Depending on the size of the mold, a single or double injection moulding machine can be used.
Injection moulding is a common technique used to create plastic containers. It has several advantages, including the ability to produce smaller batch sizes and faster production times. However, the process has some design restrictions. The materials and size of the mould must be carefully considered.
The most common shapes are round, square, and cube. These can be customized. In addition, the size and material of the mould can affect its lifespan. For instance, a thin wall food container mould has a higher lifespan than one with a thick wall. The thickness of the mould depends on the size of the boxes being manufactured.
A quality plastic food container mould can last for hundreds of thousands of shots if properly maintained. The lifespan will depend on a number of factors, including the material, size of the mould, and how the mould is used. If you are interested in a quality plastic food container mould, you should contact a leading plastic mould manufacturer.
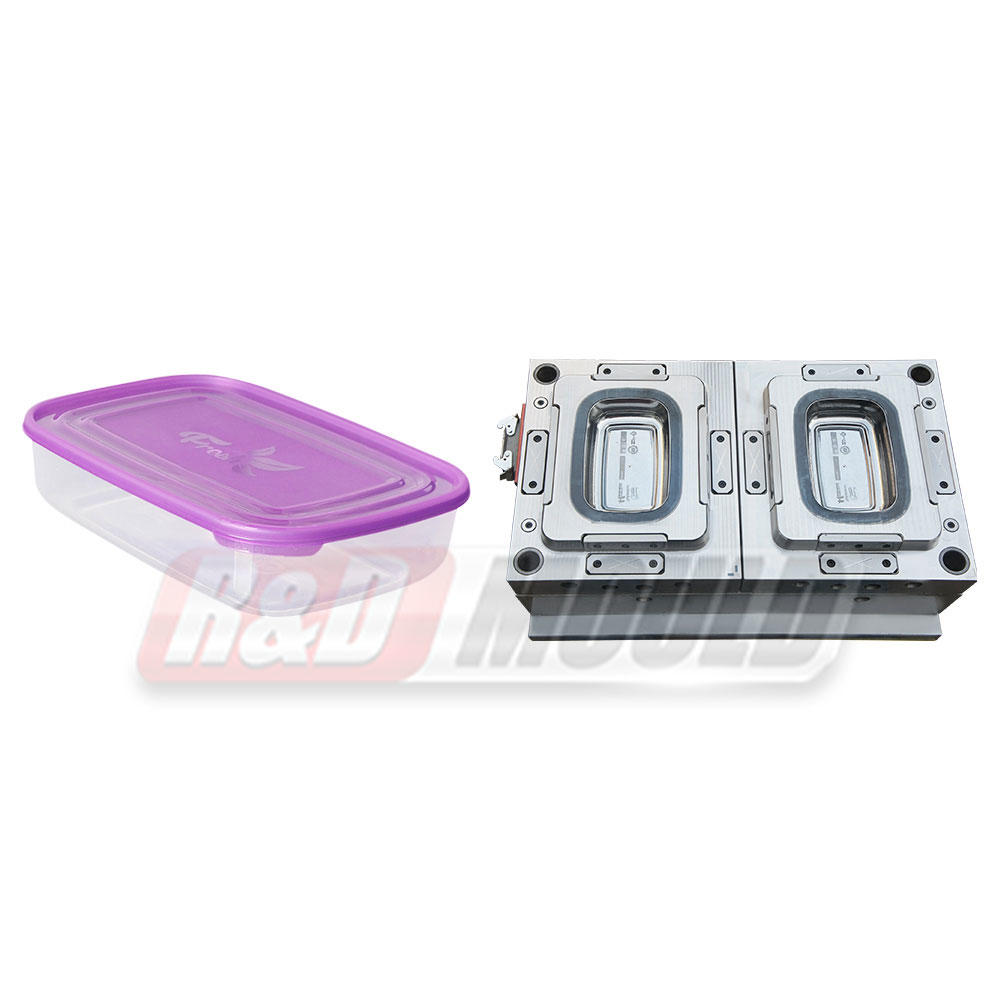
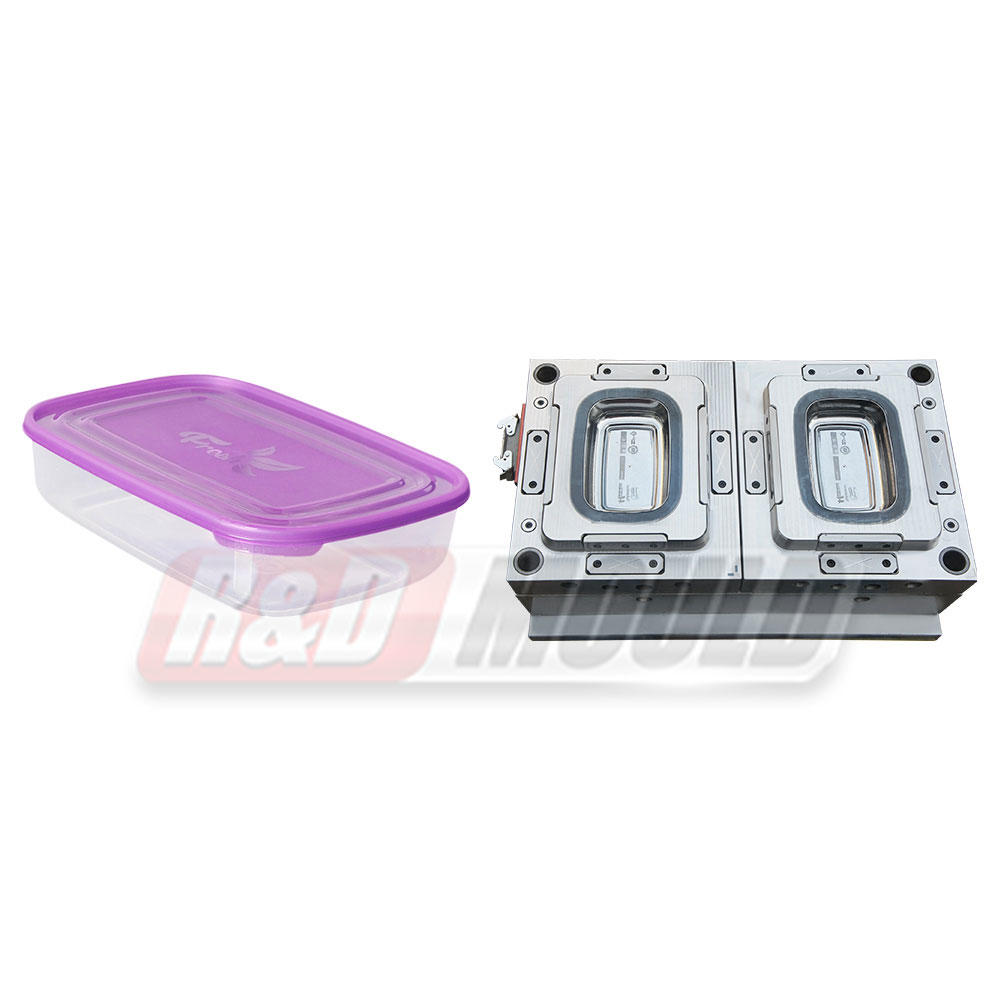